A novel technological blue hydrogen production process: industrial sorption enhanced autothermal membrane (ISEAM)
Energy Advances Pub Date: 2023-08-17 DOI: 10.1039/D3YA00090G
Abstract
A novel technological industrial blue hydrogen production process – the Industrial Sorption Enhanced Autothermal Membrane (ISEAM) process, with the potential to produce constant fuel cell grade hydrogen with a purity of 99.99%, regardless of upstream process upsets, has been modelled using an Aspen Plus simulator and MATLAB (including both thermodynamics and kinetics analysis). The process exhibits a very high hydrogen yield (99%), and methane conversion (99.9%), with a low carbon monoxide footprint (at ppm levels). The results were validated by comparing against experimental data published in the literature. Parametric evaluations were later conducted to identify the optimal operating conditions for the developed blue hydrogen ISEAM process. The required reforming heat is provided by the exothermic carbonation reaction of a sorbent, while chemical looping of the oxygen carrier (metal oxides) provides the regeneration heat required for the saturated sorbent, in a novel multi-tubular packed shell and tube reactor. Pinch analysis shows that the process is auto thermal (so it does not need any external heating utility) and can achieve an extremely high 97.5% thermal and hydrogen production efficiency. The ISEAM process was benchmarked against an industrial steam methane reforming (SMR) plant and the result shows ≥32% improvements in most of the technical parameters that were evaluated. Economic evaluation shows a levelized cost of hydrogen (LCOH) of $2.6 per kg-H2 for the baseline SMR plant compared with $1.3 per kg-H2 for the ISEAM process (a 50% cost reduction). The cost of CO2 removal (CCR) was calculated as $180 per tonneCO2 for the baseline SMR process compared with $33.2 per tonneCO2 (81.6% cost reduction) for the novel process. The novel ISEAM process utilizes mature and existing industry technologies such as desulphurization, pre-reforming, adsorption, membranes, waste heat boilers, and pressure swing adsorption. Because of this, scale-up is easier and some of the challenges associated with the SMR process and integrated sorption enhanced membrane reforming (SEMR) processes are addressed. These include thermodynamic constraints, a high energy penalty, overall process integration, optimization, membrane contamination, carbon deposition and unsteady state operation.
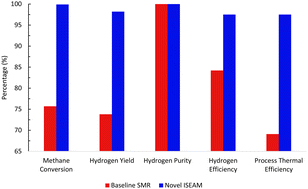
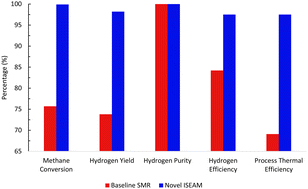
Recommended Literature
- [1] Modification of Cu–ZnO–ZrO2 catalysts with La2O3 to quantitatively tune Cu+–Cu0 dual sites for hydrogenation of dimethyl adipate to produce 1,6-hexanediol†
- [2] Sequentially optimizing carbon nanotubes framework towards flexible and compact capacitive energy storage†
- [3] Bovine plasma hydrolysates’ iron chelating capacity and its potentiating effect on ferritin synthesis in Caco-2 cells
- [4] Enantioselective reduction of N-alkyl ketimines with frustrated Lewis pair catalysis using chiral borenium ions†
- [5] Study of plasma coagulation induced by contact with calcium chloride solution
- [6] Cucurbit[7]uril host–guest complexes of the histamineH2-receptor antagonist ranitidine†
- [7] Insulating to metallic transition of an oxidized boron nitride nanosheet coating by tuning surface oxygen adsorption
- [8] One-pot synthesis of 1,4-naphthoquinones and related structures with laccase
- [9] Structural analysis of α-zirconium phosphate/cerium phosphate/graphene oxide nanocomposites with flame-retardant properties in polyvinyl alcohol†
- [10] Enhanced EDC removal from water through electron beam-mediated adsorber particle integration in microfiltration membranes†
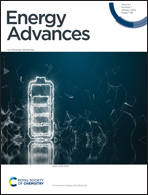
Journal Name:Energy Advances
Research Products
-
CAS no.: 2856-63-5
-
CAS no.: 96-35-5
-
3-Chloro-5-nitrobenzotrifluoride
CAS no.: 401-93-4
-
CAS no.: 367-21-5
-
CAS no.: 67-47-0
-
CAS no.: 2602-61-1
-
CAS no.: 3710-42-7
-
Methyl 4-hydroxy-3-nitrobenzoate
CAS no.: 99-42-3